Repeatability capabilities
I fear not the man who has practiced 10,000 kicks once, but I fear the man who has practiced one kick 10,000 times.
Bruce Lee
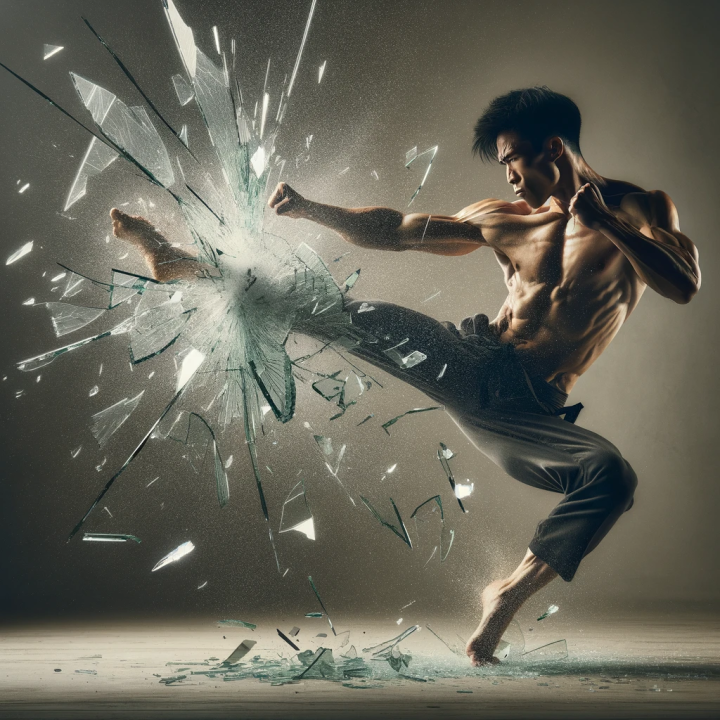
Precision, consistency and repeatability are valued everywhere and every time. It’s what makes us sharp, trustworthy and seeking for more. The photonics sector is no exception – just as everywhere else, practice makes perfect.
At OPTOMAN, we understand the importance of repeatability in laser optics manufacturing. Your customer invested in your laser system and expects nothing less than was promised. In a close market like photonics, your credibility is always on the line when delivering products. Therefore you invest in high quality, excellent performance laser optics that are crucial for your advanced laser system performance. Laser optics can not disappoint you because you can not disappoint your customer.
Imagine relying on a laser optics manufacturer that can make exceptional optics but fails to reproduce them consistently. What confidence do you have that the next batch will meet the same exact standards? And what happens when you need more of them, perhaps for scaling up or expanding your projects? Suddenly, doubt about the reliability of your system starts to emerge.
And this is where (but not only) OPTOMAN sets itself apart. We don’t just promise high-quality optics, we deliver reliability, consistency, and consequently peace of mind for you.
And this is where (but not only) OPTOMAN sets itself apart. We don’t just promise high-quality optics, we deliver reliability, consistency, and consequently peace of mind for you.

Example #1
A comparison between calculated theoretical and measurements of reflectivity of the ULLM5 coatings. Coating (IBS): Rs>99.95% & HRp>99.9% @ 1010 – 1050 nm, AOI=45° |GDD Rs|<10 fs², |GDD Rp|<20 fs²
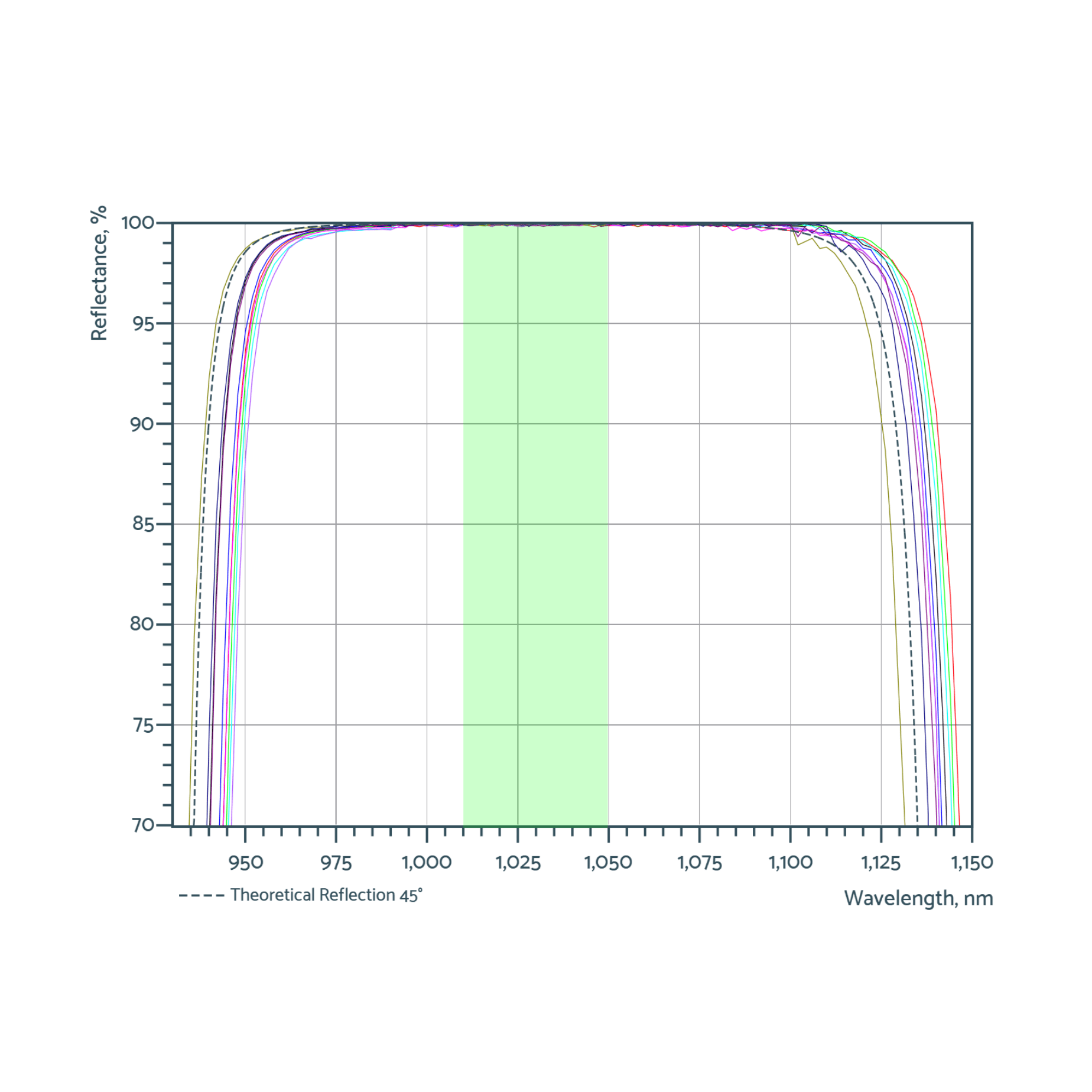
Example #2
A comparison between calculated theoretical and measurements of transmittivity of the HR+HT conversion coatings. Coatings (IBS): HT>98.5% @ 970 nm – 990 nm + R>90% @ 1030 nm, AOI=0°
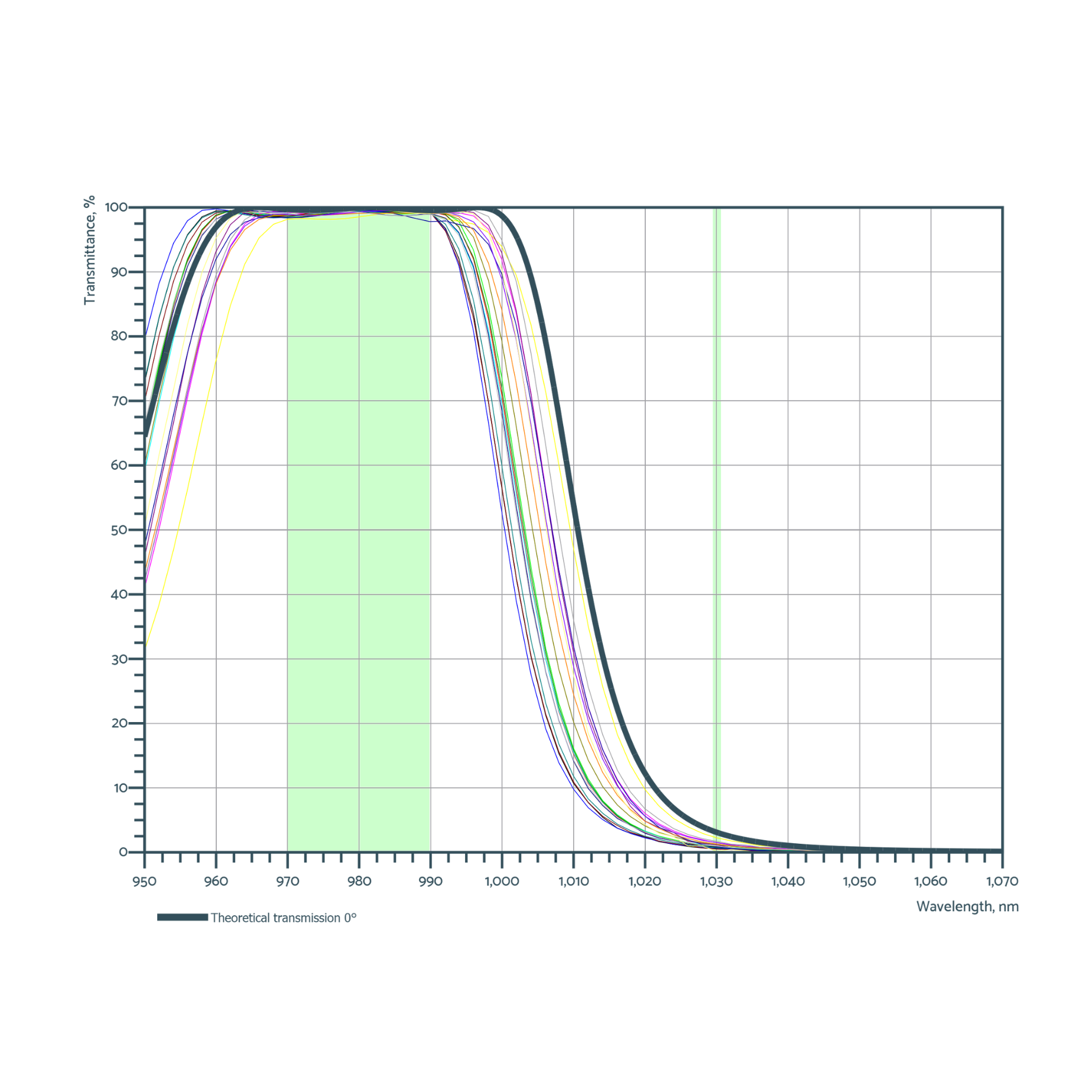
As we can see, HR+HT conversion laser optics from 14 consecutive batches possess the exact specifications. This isn’t just a testament to our technical superpowers – it’s a statement of our commitment to delivering laser optics with high confidence and most importantly, repeatability.
Because with great laser power comes great responsibility for coaters!